Testing the chemical and oil resistance of power cords is an important aspect of ensuring their durability and safety, especially in industrial or harsh environments. The specific testing procedures can vary based on the standards set forth by the regulatory bodies and organizations involved. Here's a general overview of how chemical and oil resistance testing might be conducted for power cords, including those following the Australian Standard:
Chemical Resistance Testing:
1.Selection of Chemicals:
Identify and document a comprehensive list of chemicals to which the power cord may be exposed during its operational lifespan. Consider various solvents, oils, cleaning agents, and other chemicals relevant to the cord's intended industrial or commercial application.
2.Preparation of Samples:
Prepare multiple samples of the power cord, ensuring they are representative of the actual production run. Random sampling from different batches is essential to account for manufacturing variations.
3.Exposure:
Immerse the prepared samples in individual containers containing the specified chemicals. Maintain controlled environmental conditions, including temperature and exposure duration, replicating real-world scenarios to the highest degree possible.
4.Observation:
Conduct meticulous visual inspections of the samples post-exposure. Look for any observable changes, including swelling, discoloration, cracking, softening, or deformation. Document these changes precisely and photograph the samples for a comprehensive record.
5.Physical Testing:
Perform mechanical tests, such as tensile strength, elongation, and flexibility, on both pre- and post-exposure samples. Evaluate how the chemical exposure has impacted the physical properties of the cord, ensuring it still meets the specified standards.
6.Comparison:
Analyze the before-and-after results of the visual and physical inspections. Quantify the changes observed, comparing them against predetermined acceptance criteria. Deviations from the standard specifications should be documented and analyzed thoroughly.
Oil Resistance Testing:
1.Preparation of Samples:
Carefully cut and prepare samples, ensuring consistency in size and shape. Document the origin of the samples and verify that they represent the various components of the power cord, including insulation and outer sheath.
2.Oil Immersion:
Immerse the samples in containers filled with the designated oils, ensuring complete submersion. Employ a range of oils that the power cord may encounter in its intended applications. Note the specific type of oil used for each sample.
3.Duration of Immersion:
Determine the immersion period based on industry standards and real-world usage conditions. Longer exposure times can reveal latent effects that might not be immediately apparent during shorter tests.
4.Visual Inspection:
Conduct a detailed visual examination of the samples after oil immersion. Look for changes in texture, color, surface integrity, and any signs of degradation. Record these changes systematically for further analysis.
5.Physical and Electrical Testing:
Perform rigorous physical and electrical tests on the samples, including tensile strength, flexibility, insulation resistance, and dielectric strength. Assess the impact of oil exposure on both the mechanical and electrical properties of the power cord.
6.Comparative Analysis:
Conduct a meticulous comparative analysis of the pre- and post-exposure test results. Evaluate the extent of changes in physical and electrical properties. Deviations from the specified standards should be thoroughly investigated, and the impact on the cord's performance and safety must be clearly documented.
T4/T3 Australian Standard Power Cord
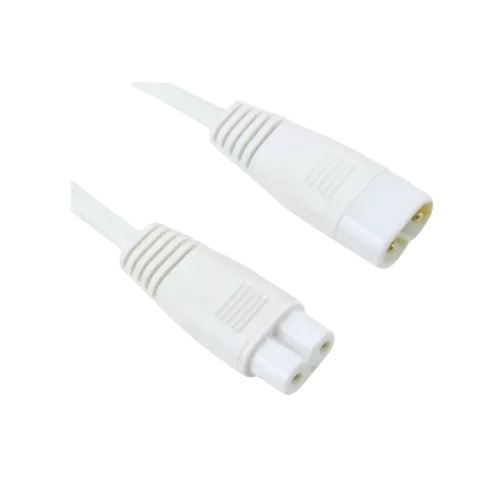
T4/T3 Australian Standard Power Cord
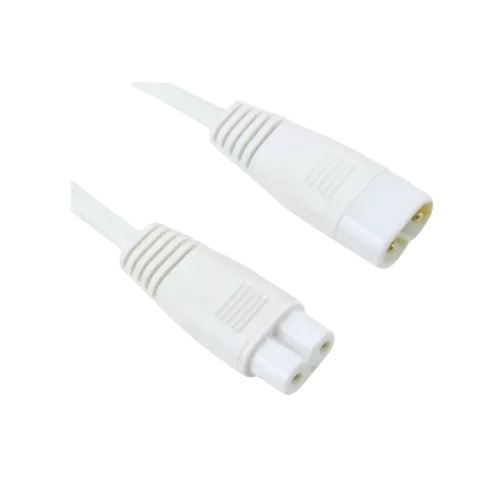