To address heat dissipation and insulation in the three-core national standard plug product suffix power cord, several design considerations and features may be implemented:
Insulation Materials: The power cord meticulously selects insulation materials based on a thorough analysis of dielectric properties. This involves considering factors such as breakdown voltage, thermal stability, and resistance to environmental elements. Commonly used materials include PVC, XLPE, or ethylene propylene rubber (EPR), chosen for their ability to maintain effective insulation and prevent electrical leakage even in demanding conditions.
Conductor Design: The three-core configuration's conductor design goes beyond mere cross-sectional enlargement. Engineers may adopt sophisticated conductor materials like high-purity copper or aluminum alloys, optimizing not only for electrical conductivity but also for enhanced thermal conductivity. This dual-focus aims to minimize resistive losses and, consequently, heat generation during power transmission.
Temperature Ratings: Temperature ratings for each component undergo meticulous testing in controlled environments. This involves subjecting the cord to varying temperatures to evaluate its performance under stress. The result is a precise determination of the cord's operational limits, providing users with clear information about the maximum temperatures the cord can withstand without compromising safety or functionality.
Heat-resistant Sheathing: The outer sheathing of the power cord is a masterpiece in material engineering. It typically employs advanced polymers like thermoplastic elastomers (TPE) or silicone rubber, chosen not just for their heat resistance but also for their flexibility and durability. This sheathing acts as a robust barrier, shielding the internal components from extreme temperatures and external stressors.
Thermal Protection Devices: The incorporation of thermal protection devices involves intricate circuitry and precise calibration. Fuses, for instance, are selected based on their response times and current-carrying capacities. Temperature-sensitive switches are strategically positioned to detect localized heating, triggering a rapid response to isolate the affected section and prevent any potential cascading failures. This level of detail ensures a fail-safe system that reacts swiftly to protect both the cord and connected devices.
Testing and Certification: Testing procedures extend beyond standard protocols, encompassing accelerated aging tests, thermal cycling, and simulations of extreme operating conditions. Certification from authoritative bodies involves an exhaustive review of these test results, scrutinizing every aspect of the cord's performance. The certification process acts as a stringent gatekeeper, allowing only products that have demonstrated unparalleled adherence to safety standards to reach the market.
Design for Airflow: The design's emphasis on airflow management is akin to an aerodynamic engineering marvel. Computational fluid dynamics (CFD) simulations may be employed to optimize conductor spacing, sheathing contours, and overall cord geometry. This ensures not only that heat dissipates efficiently but also that the cord operates within a temperature profile conducive to long-term reliability.
Quality Control Measures: Quality control is a multi-faceted process involving statistical process control (SPC), in-line testing, and rigorous end-of-line inspections. Automated vision systems may scan for microscopic defects, and machine learning algorithms can predict potential issues based on historical data. This level of sophistication in quality control instills confidence that each power cord leaving the manufacturing facility is not just a product but a testament to uncompromising quality.
Continuous Monitoring: In cutting-edge designs, continuous monitoring involves a sophisticated network of sensors and microcontrollers. These sensors are strategically placed at critical points to capture real-time data on temperature variations. Machine learning algorithms analyze this data, predicting trends and proactively implementing adjustments. This dynamic, self-regulating system ensures that the power cord not only reacts to immediate threats but also evolves its performance over time, constantly optimizing for safety and efficiency.
P3-10 Three-core national standard plug product suffix power cord
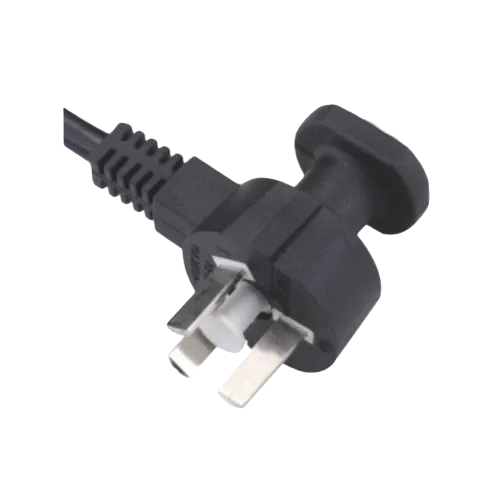
P3-10 Three-core national standard plug product suffix power cord
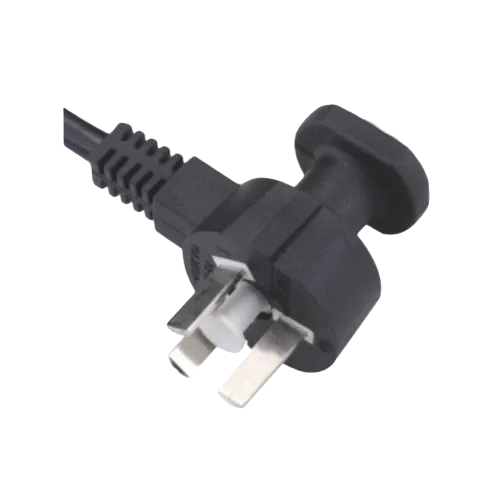