The design of a UK standard computer power cord plays a crucial role in determining its resistance to wear and tear in a professional setting. Several design factors contribute to the overall durability and longevity of the power cord in such environments:
Materials: The outer insulation of the power cord must boast top-tier materials such as industrial-grade PVC or TPE. These materials don't just resist abrasion and chemicals; they undergo rigorous testing to ensure they maintain their structural integrity over prolonged use in challenging professional contexts. The molecular composition of these materials is fine-tuned to balance flexibility, durability, and resistance to environmental stressors.
Strain Relief: The strain relief mechanism is not merely robust; it's a masterpiece of engineering. This involves the integration of reinforced materials strategically positioned around connector joints, meticulously designed to absorb stress. Finite element analysis ensures that these components can withstand a multitude of forces, from the subtle tension of regular use to the abrupt jolts that can occur in dynamic professional settings.
Flexibility: Achieving the optimal balance between flexibility and sturdiness requires a blend of material science and design finesse. The power cord is engineered to be not just pliable but elegantly so, ensuring it can effortlessly navigate the intricate landscapes of professional environments. This flexibility is not just a design choice; it's a calculated engineering feat that enables the cord to endure constant movement, twists, and turns without succumbing to fatigue.
Cord Thickness: The insulation thickness isn't a mere specification; it's a shield of resilience. The power cord's outer layer isn't just thick; it's engineered to be a formidable barrier against physical stress. Computational simulations and stress testing validate that the thickness of the insulation is not just compliant with standards but exceeds them, providing an extra layer of protection against wear, tear, and external elements.
Connector Quality: Connectors aren't just endpoints; they are the vanguards of reliability. Crafted from premium materials with precision molding techniques, these connectors go through a battery of tests. Their attachment to the cable is more than secure; it's an engineering marvel that ensures they can endure countless insertions and removals without showing any signs of wear. This level of connector quality isn't a luxury; it's a standard that defines the power cord's reliability.
Twist Resistance: Twist resistance isn't a feature; it's a testament to the power cord's internal architecture. Internal components aren't just resistant to twisting; they are strategically positioned to minimize the impact of torsional forces. Finite element simulations and real-world stress tests ensure that the power cord doesn't just endure frequent repositioning; it thrives in dynamic professional settings, where twists and turns are part of the daily routine.
Abrasion Resistance: The outer layer's resistance to abrasion isn't a coating; it's a shield of resilience. Materials with reinforced properties form an exterior that's not just resistant to scratches; it's a fortress against the harshest environments. Rigorous abrasion tests validate that the power cord isn't just resilient; it's prepared to withstand the daily onslaught of rough surfaces, sharp edges, and unpredictable conditions.
Temperature Resistance: Temperature resistance isn't a passive quality; it's an active defense mechanism. The power cord doesn't just endure extreme temperatures; it thrives in them. Advanced materials with tailored thermal properties ensure that the cord remains resilient in scorching heat and sub-zero cold. Thermal cycling tests prove that the power cord doesn't just adapt to temperature fluctuations; it conquers them, emerging unscathed and ready for more.
JT006-UK standard Computer Power Cord
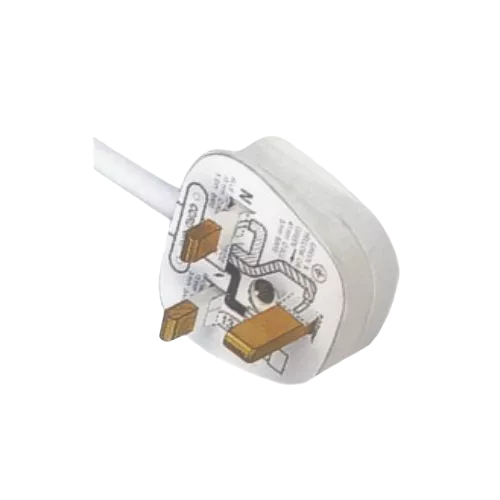
JT006-UK standard Computer Power Cord
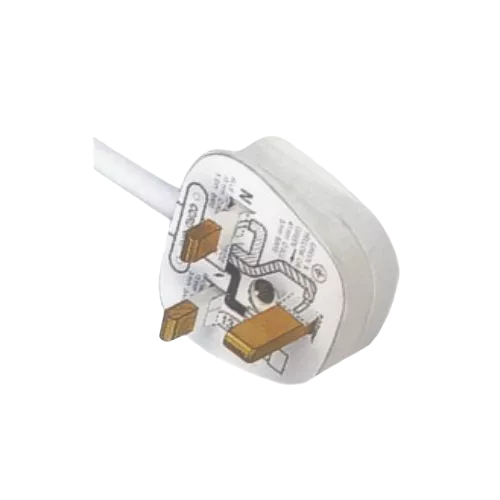